技術情報
プレマテックの技術力
市場競争が激化する中、最適な技術・商品戦略と組織マネジメントの仕組みを構築する「コア技術戦略」をプレマテックでは、重要視しています。
1951年の創業以来、治工具、専用機、LCD製造装置など様々なものづくりをして参りました。設計・部品加工・組立・現地対応を一貫して行う生産体制で、各種製造装置の開発・生産に於いて高いサービスを提供しています。
自社一貫生産体制
多様な商品に応用することによって、コア技術を鍛え技術的な組織能力を構成する知識の多くは、技術者に属人的な形で蓄積されてきました。 60年間に渡り多くの商品開発に取組むことで、多くの技術者が技術・商品開発において試行錯誤を経験。企業として、コア技術を形成する知識体系は、深さ・広さが増し、質的にも高度なものに深化してまいりました。
現在、弊社が提供しているラビング装置は鮮明な画質を要求されているタブレットや液晶TV製造に欠かせない装置で世界シェアの80%以上を独占。
現行の技術は改善・深化すると同時に、いくつかの新しい技術が加えられています。このようなプロセスを経ることによって、特定の技術に企業固有の組織能力が構築されてきました。 このように蓄積・構築された体系的な知識こそが、世界に認められたプレマテックの「コア技術」なのです。
「コア技術」の深化・進化
- 多用な商品を
次々と開発 - ノウハウ
技術力の蓄積 - より広く
より深い
コア技術へ - 世界シェア
80%の
ラビング装置へ
要素技術
市場競争が激化する中、最適な技術・商品戦略と組織マネジメントの仕組みを構築するコア技術戦略として、五つの要素技術[擦る][塗る][搬送する][貼る][纏める]を元に、トータルソリューションビジネスの展開を図っております。
「擦る」
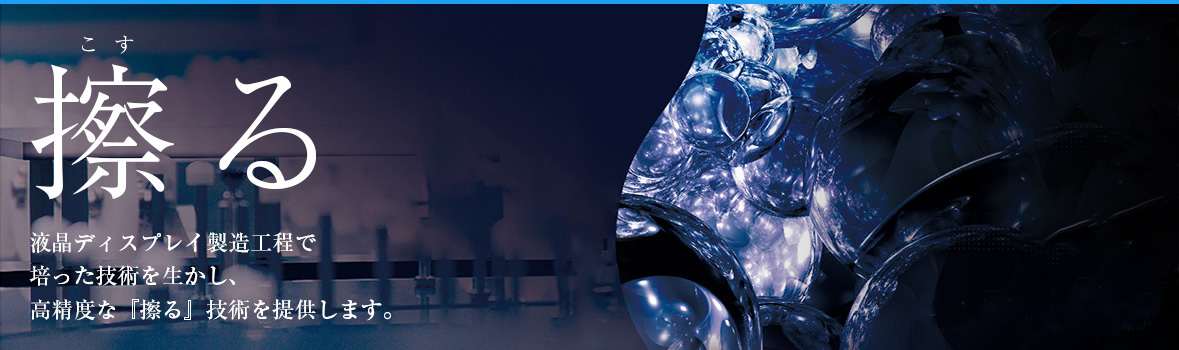
-
特徴
1
均一に擦る
- 独自の『逆クラウン加工』により、ローラーの撓み量を10µm以下に加工
- 『擦る』際の摩擦力をトルク値として検出し、一定のトルク値となるよう自動補正
-
特徴
2
大型ワークを擦る
- 特殊加工された鋳物ステージベースの採用により、大型ステージでも変形量を最小化
- 3,000mm x 6,000mm 対応の超大型研磨機で、ステージ平面度を20μm以下に研削加工
-
特徴
3
任意の角度で擦る
- ローラーとステージの角度を、0.1°単位で設定することが可能
- 2,550mm x 2,550mm (総重量2,500kg)の超大型回転ステージを製作
当社技術の採用例
採用工程 | 液晶ディスプレイ製造工程 |
---|---|
装置名称 | ラビング装置(RLシリーズ) |
設備概要 | パフ材を巻きつけたローラーでポリイミド膜を『擦る』ことにより、液晶分子を一定方向に配列させるための溝を加工します。 |
設備仕様
ローラー最大寸法 | φ140mmx4,000mmL |
---|---|
ローラー最高回転数 | 2,000rpm |
ローラー角度設定範囲 | ±47° |
ローラー押込み量の分解能 | 0.001mm |
ステージ最大寸法 | 2,550mm x 2,550mm |
ステージ最高移動速度 | 1,000mm/sec |
ステージとローラーの隙間精度 | ±0.005mm |
静電気対策 | 加湿器、軟X線、イオナイザー |
「塗る」
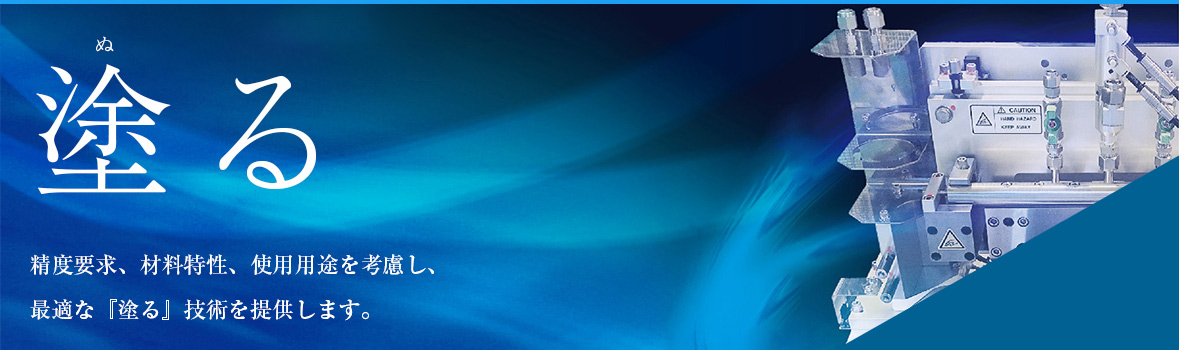
-
特徴
1
任意パターンを塗る
- フレキソ印刷方式は、版のデザインを変更することで任意パターンを塗ることが可能
- 0.00007mmの薄膜(ポリイミド膜)を面内分布±5%で塗布
-
特徴
2
全面パターンを塗る
- スリットコート方式は、スリットダイの長さを変更することで全面パターンを塗ることが可能
- 150,000cpsの高粘度材料(UV硬化材)を膜厚100μmで塗布
-
特徴
3
線パターンや点を塗る
- ディスペンス方式は、プログラムの変更で任意の線パターンや点を塗ることが可能
- 用途や材料粘度に応じて、エアー加圧方式やメカニカル方式の選択が可能
当社技術の採用例
採用工程 | ディスプレイ製品の組立工程 |
---|---|
装置名称 | スリットコーター(SCシリーズ) |
設備概要 | スリットダイで光学性透明接着剤を『塗る』ことにより、カバーガラスとディスプレイを貼り合わせるための前処理をします。 |
設備仕様
スリットダイ最大寸法 | 1,000mm |
---|---|
スリットダイ仕様 | ステンレス(内部研磨) |
塗布方式 | ステージ移動式、ヘッド移動式 |
ステージ速度範囲 | 5~600mm/sec |
塗布幅の変更 | シムプレートの交換 |
塗布厚の範囲 | 0.1~0.8mm |
材料貼度の対応範囲 | MAX.150,000cps |
材料加圧方式 | エアー加圧、メカニカルポンプ |
「搬送する」
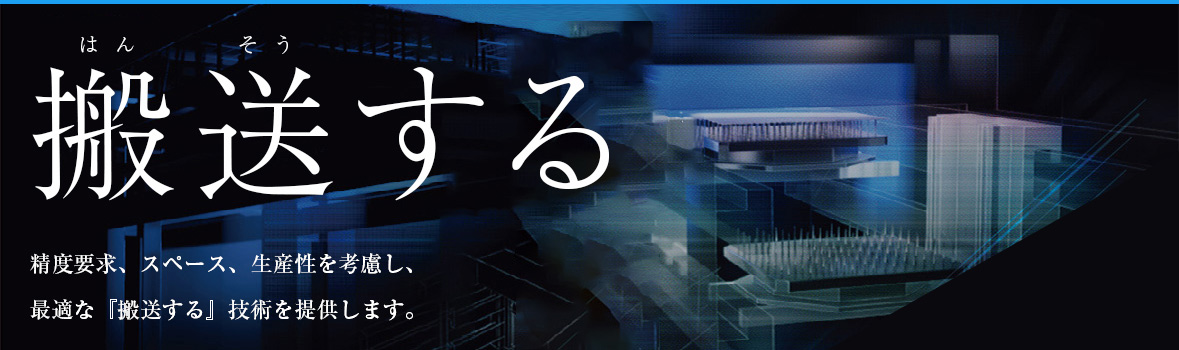
-
特徴
1
コンベアで搬送する
- 0.12mmの薄いフィルム、2,200mmx2,500mmの大型ガラスの搬送を実現
- CCDカメラを搭載した高精度アライメント機能、任意角度への回転機構に対応
-
特徴
2
ステージで搬送する
- 平面度20μmのフラットステージ、静電気対策に有効なピンステージをラインナップ
- ピッチング精度±0.05°、ヨーイング精度±0.02°の高精度搬送に対応
-
特徴
3
SCARAで搬送する
- 限定された設計範囲や可搬重量に合わせたSCARA搬送の設計・製作が可能
- 既成SCARAロボットを搭載した上位通信システム対応の搬送システム製作
当社技術の採用例
採用工程 | 液晶ディスプレイ製造工程 |
---|---|
装置名称 | 光配向用搬送システム(PAシリーズ) |
設備概要 | 紫外線照射装置の下を大判ステージで高精度かつ安定して『搬送する』ことにより、液晶分子を一定方向に配列させるための配向処理をします |
設備仕様
対応ワークサイズ | 2,200mm x 2,500mm |
---|---|
装置タイプ | シングル搬送、ツイン搬送、シームレス搬送 |
ステージ方式 | フラットステージ、ピンステージ |
ステージ駆動方式 | リニアモータ |
ステージ最高移動速度 | 1,000mm/sec |
ステージ回転角度 | ±15° |
ステージヨーイング精度 | ±0.2° |
ワーク位置決め機能 | CCDカメラによる自動アライメント搭載 |
「貼る」
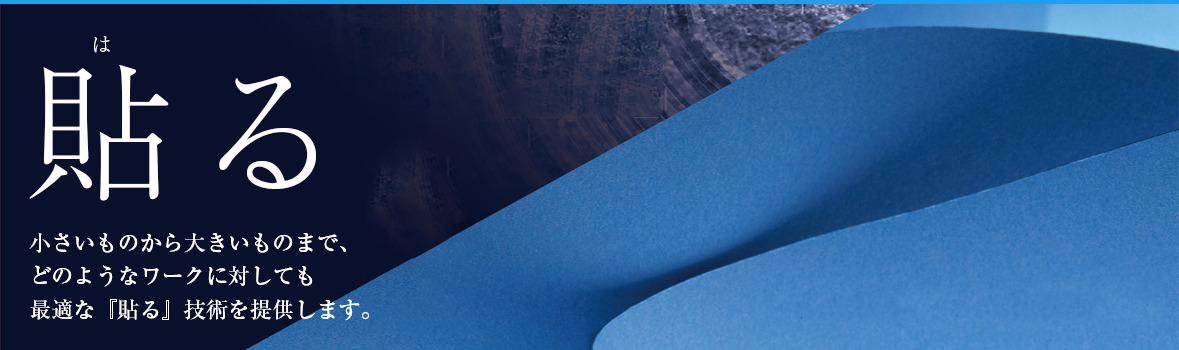
-
特徴
1
大気中で貼る
- ステージ反転方式とローラー方式のどちらかでも、大気中で気泡混入のない貼り合わせを実現
- ガラス、フィルム、ディスプレイなど、幅広い製品に貼ることが可能
-
特徴
2
真空中で貼る
- 0.4Paの真空環下で、位置制御、トルク制御による貼り合わせが可能
- 真空中でもCCDカメラを使った上下ワークの位置合わせ精度±5μm以下を実現
-
特徴
3
大型ワークを貼る
- 接着剤の塗布、高精度アライメント、大型真空チャンバーによる貼り合わせ機能を盛り込んだ、65インチのディスプレイへ特殊レンズを貼る量産自動化ラインの製作実績
当社技術の採用例
採用工程 | ディスプレイ製品の組立工程 |
---|---|
装置名称 | 貼り合せ装置(KAR10) |
設備概要 | UV硬化型の透明接着剤を塗布し、大気中または真空中で『貼る』ことにより、ディスプレイにカバーガラスやタッチパネルを気泡なく貼り合せます。 |
設備仕様
対応ワークサイズ | 7~10インチ |
---|---|
対応ワーク種類 | 液晶ディスプレイ+タッチパネル・カバーガラス |
貼り合せ環境 | 大気中・真空中の選択可能 |
チャンバー真空度 | 10Pa |
接着材塗布方式 | スリットコート |
接着剤硬化方式 | UV照射機能を組込み(仮固定) |
ワーク厚み補正 | 厚みを測定し、データに基づいて自動補正 |
ローダー/アンローダー | 追加で設置可能※オプション |
「纏める」
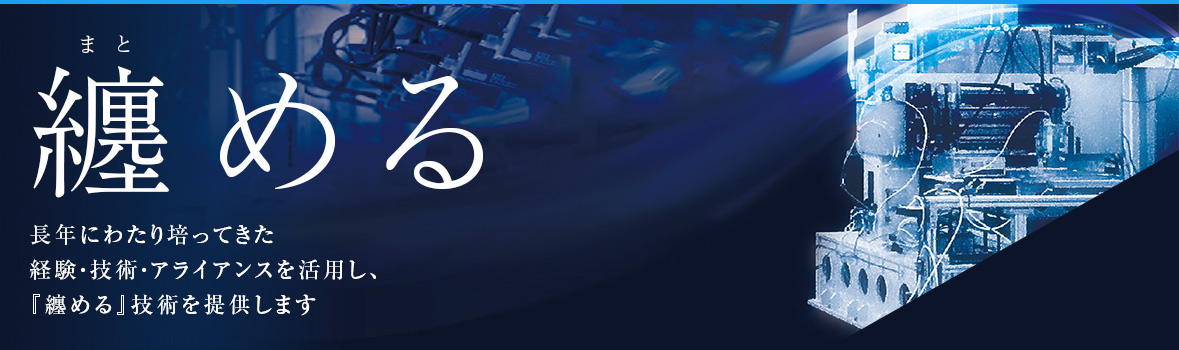
-
特徴
1
プロセスを纏める
- 工場内に各種テスト用設備・測定器を完備しており、事前のプロセス検証が可能
- 検証結果に基づいて、最適なプロセスを実現するための技術と設備を提案
-
特徴
2
ラインを纏める
- プロセス設備だけではなく、前後装置や搬送装置などを合わせたライン提供が可能
- タクトタイムや生産性を考慮し、無駄のない最適なレイアウト提案
-
特徴
3
アライアンスで纏める
- アライアンス企業と共同で、工場全体のラインとプロセスの提供が可能
- 弊社がアライアンス企業をまとめるので、お客様の負担を大幅に軽減
当社技術の採用例(1)
採用工程 | 液晶ディスプレイ製造工程 |
---|---|
装置名称 | セル工程ライン |
設備概要 | パターニング・配向膜の形成・貼り合せライン |
当社技術の採用例(2)
採用工程 | タッチパネル製造工程 |
---|---|
装置名称 | パターニングライン |
設備概要 | ITO膜と金属膜のパターニングライン |